Производство плитки вибропрессованием
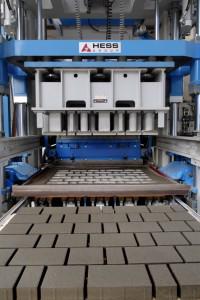
Технология объёмного вибропрессования базируется на методе получения изделий из бетона посредством виброуплотнения полусухой смеси с пригрузом формующего пуансона.
Производство вибропресованных изделий:
— требует наличия стационарного вибропресса
— осуществляется на основе виброуплотнения полусухих бетонных смесей с пониженным водоцементным отношением
— позволяет получать высокопрочные изделия с отличными показателями морозостойкости (>F-300) и водопоглощения (<5%) при уменьшенном содержании цемента марки М-400.
— предоставляет возможность получения изделий (бордюров, плитки, водоотливов, стеновых и перегородочных камней) с точными геометрическими размерами и стабильными основными эксплуатационными параметрами.
За формовку изделий отвечают матрица (стенки плитки) и пуансон (поверхность плитки и рисунок на ней) вибропресса. Формуется продукция на сменных поддонах, на которых впоследствии осуществляется и сушка.
Условно производство вибропрессованных изделий разделяют на три этапа:
1) Приготовление бетона. Здесь, как и на первом этапе производства тротуарной плитки методом вибролитья, потребуется бетоносмеситель принудительного действия: для получения однослойных изделий — один, для двухслойных — два.
2) Формование. Приготовленный бетон подаётся в матрицу вибропресса, которая прижимает поддон к виброплощадке. Непосредственно после загрузки формовочной смеси, опускается пуансон и запускается процесс вибропрессования. Длится он порядка 3–5 секунд: этого времени достаточно для того, чтобы под воздействием вибрации материал уплотнился. Затем пуансон с матрицей поднимаются, оставляя на виброплощадке технологический поддон с отформованными изделиями. Этот поддон снимается и подаётся на участок сушки, а его место занимает другой и операция повторяется.
3) Сушка. На участке сушки изделия проходят тепловлажностную обработку: как правило, для этого используется водяной пар. Но в случае наличия свободных производственных площадей сушка изделий может производиться и без тепловой обработки.
Когда прочность бетона достигнет 1,5 — 2 МПа, изделия можно снимать с поддонов и использовать последние в новом цикле производства. Отвердевание бетона до нужного показателя, в среднем, происходит за 6–7 часов.
Итак, минимальный набор оборудования, необходимого для организации производства вибропрессованных изделий, таков:
- Один или два бетоносмесителя принудительного действия.
- Вибропресс.
- Комплект технологических поддонов (поддоны можно изготовить самостоятельно).
- Источник тепла для оснащения участка сушки в холодное время года.
Соблюдение рекомендованной рецептуры гарантирует получение тротуарной плитки, показатели прочности, истираемости, водопоглощения и морозостойкости которой полностью удовлетворяют настоящим требованиям ГОСТ 17608–91.
Сравнивая технологии производства тротуарной плитки вибролитьём и вибропессованием, можно отметить следующие преимущества последнего перед первым:
— большая прочность изделий при меньшем расходе цемента;
— Значительная экономия на пластификаторе и модифицирующих добавках
— малая доля ручного труда
— возможность организации масштабного производства при снижении общих расходов, что достигается благодаря сокращённому технологическому циклу и двухсменной работе. К тому же, большинство неавтоматизированных вибропрессов, при необходимости расширения производства, можно дооснастить теми или иными приспособлениями для увеличения производительности.
Просмотров: 8606